Factors to consider when welding thin to thick sections
Are you a welder who often works with welding thin to thick sections? If so, you know firsthand the challenges of such projects. Having the right equipment at your disposal is crucial to ensuring seamless and strong welds. Investing in a quality welder that can handle varying metal thicknesses is essential. Let’s explore key factors when choosing a welder for welding thin to thick sections.
First and foremost, versatility is key. You need a welder that effortlessly adapts to different metal thicknesses. Look for a welder that offers a wide range of amperage settings, allowing you to weld thin and thick sections precisely. This flexibility saves you time and effort by eliminating the need for multiple welders or constant adjustments.
Another factor to consider is control. Welding thin to thick sections requires finesse and accuracy. Look for a welder with precise control over the arc and heat output. This ensures you maintain optimal welding conditions throughout the process, minimizing the risk of burn-through or lack of fusion. Smooth and controlled arcs enable you to achieve high-quality welds on thin, thick metal sections.
Additionally, portability is important, especially if your welding projects take you to various locations. Opt for a lightweight and compact welder without compromising on performance. This allows you to transport and maneuver the equipment easily, saving time and energy. A portable welder also ensures you can conveniently tackle welding jobs in different settings, whether on-site in construction or repair projects.
Consider the availability and compatibility of accessories and consumables as well. When working on thin to thick sections, using the right consumables, such as different types and sizes of electrodes, can significantly impact the quality and efficiency of your welds. Make sure that the welder you choose offers a variety of readily available accessories and consumable options. This ensures that you are well-equipped to handle any welding challenge that comes your way.
Lastly, safety should always be prioritized. Welding involves high temperatures and electrical currents, so safety features are crucial. Look for a welder that offers thermal overload protection, voltage fluctuation protection, and proper grounding options. These safety features not only protect you but also prolong the lifespan of your equipment.
In conclusion, welding thin to thick sections requires careful consideration of various factors when choosing a welder. Versatility, control, portability, availability of accessories, and safety features should be at the forefront of your decision-making process. By investing in a welder that excels in these areas, you can tackle any welding project with confidence and efficiency. So, don’t compromise on quality and equip yourself with a reliable welder that helps you unlock your full welding potential.
Material properties
Are you a skilled welder looking to upgrade your equipment and take your craft to the next level? Look no further! Our top-quality welders are designed with all the needed features, making them perfect for working with various materials.
Understanding material properties is key to achieving strong and durable welds. Every material has unique characteristics, and a reliable welder is essential to ensuring successful and efficient bonding.
Our welders are built to handle various materials, from stainless steel and aluminum to mild steel and cast iron. You can count on our machines to deliver precision welding, regardless of your working material.
One of the crucial factors in welding is heat control, and our welders excel in providing optimal temperature settings for various materials. With our advanced technology and adjustable heat controls, you can achieve perfect welds on any metal, maintaining its integrity and strength.
Another vital aspect of material properties is their thickness. Different materials come in various gauges; welding them requires a welder that can adapt to these thicknesses. Our welders offer versatile settings, allowing you to weld materials of different gauges without compromising quality.
Durability is an essential factor to consider when purchasing a welder. You need a machine that can withstand demanding environments and continuous welding. Our welders are manufactured with robust components, ensuring reliability and longevity. You can trust our machines to accompany you throughout your welding journey, project after project.
Safety is of utmost importance in any welding operation. Our welders have built-in safety features, including overheat protection and automatic shut-off systems. These features are designed to keep you safe and minimize any potential accidents during the welding process.
Additionally, our welders are user-friendly, making them suitable for welders of all skill levels. Whether you are a seasoned professional or just starting your welding adventure, our machines are designed to be easy to use, ensuring a smooth and hassle-free welding experience.
Investing in a high-quality welder is an investment in your future as a skilled welder. With our reliable and versatile machines, you can confidently tackle any welding project, knowing you have the right tool. Don’t compromise on the quality of your work; choose our welders to elevate your welding capabilities and achieve outstanding results every time.
So, why wait? Join the community of satisfied welders who have chosen our brand as their go-to welding solution. Browse our range of welders and take the first step toward improving your craft. Our top-notch products, expert support, and unparalleled performance won’t disappoint you. Empower your welding skills today with our superior welders and witness the difference for yourself!
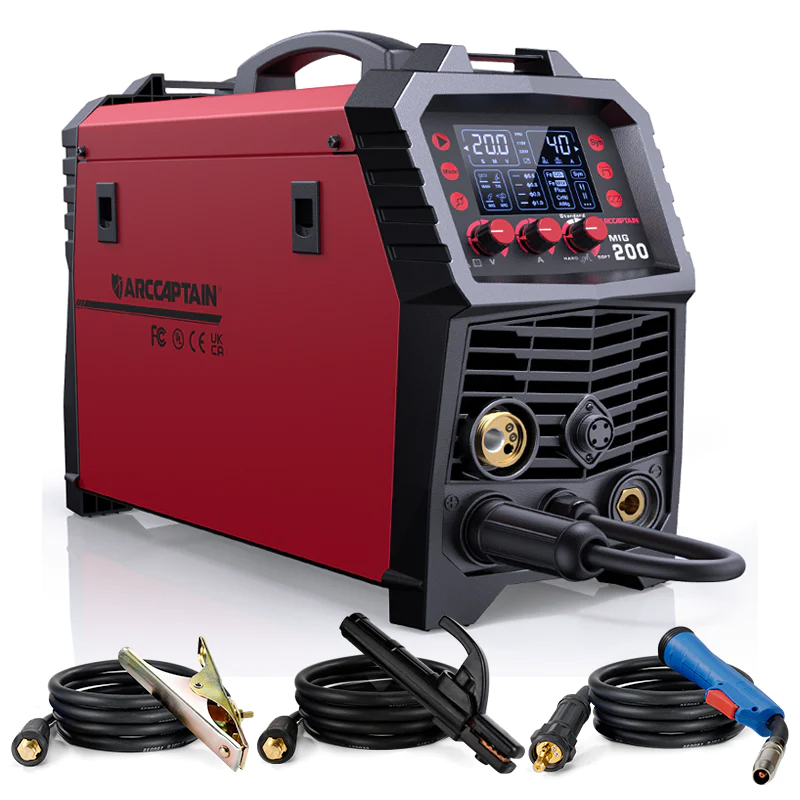
Thermal conductivity
Hey there, fellow welder enthusiasts! Are you looking to enhance your welding skills? Well, let’s discuss one of the essential factors you should consider when purchasing a welder: thermal conductivity.
You might wonder why thermal conductivity is vital in your welding projects. Allow us to shed some light on this matter. Thermal conductivity refers to the ability of a material to conduct heat. In simpler terms, it determines how efficiently heat transfers from one point to another within the welder.
Thermal conductivity is crucial to welding’s optimal performance and precision. Different metals have varying thermal conductivities, transferring heat at different rates. A welder with excellent thermal conductivity enables you to manage heat distribution effectively and achieve high-quality welds.
Let’s bring this concept closer to home. Imagine you’re working on a project involving aluminum or copper. These metals are known for their excellent thermal conductivity. A welder that matches their thermal properties would work in your favor, allowing heat to spread evenly throughout the workpiece. This ensures a consistent weld with minimal distortions and avoids any potential defects.
On the other hand, if you’re dealing with metals like stainless steel or cast iron, you may face challenges due to their relatively lower thermal conductivity. In such cases, a welder with superior thermal conductivity becomes your greatest ally. It helps compensate for the reduced heat transfer in these materials, enabling you to achieve the desired weld strength and integrity.
Investing in a welder with optimal thermal conductivity benefits your projects immensely. It enhances your welding skills and saves you time and effort. Thanks to efficient heat distribution, you’ll experience improved arc stability, increased welding speed, and reduced instances of rework. Ultimately, this translates into higher productivity and a more satisfying welding experience.
So, dear welding world, consider thermal conductivity when considering your next welder purchase. Ensure that the model you choose aligns with the projects you frequently undertake. Doing so will equip you with a powerful tool that will take your welding endeavors to new heights.
Remember, a welder with excellent thermal conductivity is your secret weapon for accomplishing impeccable welds and leaving a lasting mark in the welding realm. Happy welding, and may your projects be nothing short of extraordinary!
Base metal thicknesses
Are you a professional welder or a passionate DIY enthusiast? No matter which category you fall into, one thing is for sure: you need a reliable and efficient tool to bring your welding projects to life. That’s where a top-notch welder comes into the picture. Whether working on automotive repairs, construction projects, or crafting intricate metal art, having the right welder can make all the difference.
Understanding base metal thicknesses is key to ensuring the success of your projects when it comes to welding. The thickness of the base metal you’re working with determines the type of welding process you should employ and the specifications of your small welding machine. This knowledge is crucial in achieving strong, durable, and aesthetically pleasing welds.
Different welding processes offer distinct advantages depending on the thickness of the base metal. MIG (metal inert gas) welding is an excellent choice for thinner metals. This process utilizes a continuously feeding wire electrode, shielding the weld pool from contaminants and providing a stable arc. MIG welding is known for its versatility and is favored by many professionals and hobbyists.
On the other hand, thicker materials demand a more robust welding process, such as Stick welding (also known as Shielded Metal Arc Welding or SMAW). This method employs a consumable electrode coated in flux, which releases gas to protect the weld metal. Stick welding is known for its ability to handle heavy-duty applications, making it ideal for construction and repair projects involving thicker base metals.
Of course, the success of your welding projects doesn’t solely rely on the welding process. Selecting the right welder that can accommodate different base metal thicknesses is equally vital. A good welder should offer various amperage ranges, ensuring compatibility with wide base metal thicknesses. Look for welders with multiple power settings that adjust the amperage accordingly, granting you the flexibility to tackle various welding tasks.
Furthermore, consider the duty cycle of the welder you will invest in. The duty cycle represents how long a welder can operate before needing to cool down. High-quality welders usually come with a higher duty cycle, guaranteeing longer continuous welding sessions and reducing the risk of overheating. This feature is particularly important when working with thicker base metals that might require more welding time.
In conclusion, your success as a welder depends on your chosen tools. Understanding base metal thicknesses and using the appropriate welding process ensures your welds’ strength, durability, and quality. Investing in a versatile welder that can handle a wide range of base metal thicknesses empowers your projects and enhances the quality of your craftsmanship. So, why wait? Purchase a reliable welder today and witness the incredible results for yourself!
Filler metal selection
Choosing the Right Filler Metal: Enhancing Your Welding Performance
As a welder, you know that achieving flawless welds that stand the test of time is essential. Your expertise lies in your skills and technique and in the equipment you choose. When it comes to welders, selecting the right filler metal is key to ensuring the durability and strength of your welds.
The filler metal acts as a bridge, joining the base metals together. It gives your welds the necessary strength and stability, allowing them to endure harsh conditions and heavy usage. People often overlook the importance of filler metal selection, but it can make all the difference in the world regarding the quality of your welds.
One critical factor to consider when choosing the right filler metal is the type of metal you’ll be welding. Different metals require different filler metals to form robust bonds. For example, when welding stainless steel, a filler metal like ER308L provides excellent corrosion resistance, perfect for applications where durability is paramount. On the other hand, when working with mild steel, ER70S-6 offers superb strength and results in enhanced weld characteristics.
Another critical factor to consider is the welding process you’ll be using. Whether you’re utilizing MIG, TIG, or stick welding, each method has specific requirements regarding filler metal selection. Understanding these requirements and selecting the appropriate filler metal ensures optimal weld quality and performance.
Furthermore, you’ll also need to consider the environmental conditions to which your welds will be exposed. If your projects involve applications that face extreme temperatures, high humidity, or corrosive substances, choosing a filler metal with exceptional resistance to these elements is crucial to maintaining the integrity of your welds over time.
At Arc Captain, we understand the significance of selecting the right filler metal for your welding needs. That’s why we offer a wide range of top-quality filler metals tailored to suit diverse welding applications. Our filler metals undergo rigorous testing to guarantee their performance and durability, giving you peace of mind that your welds will withstand even the harshest conditions.
Choose the correct filler metal to take your welding projects to the next level. Don’t compromise on your welds’ strength, longevity, and reliability. Invest in a high-quality filler metal from Arc Captain and witness its transformative impact on your welding performance. Your welds will not only meet industry standards but also exceed your expectations. Start enhancing your welding today and experience the difference that proper filler metal selection can make!
Welding process
Looking for a reliable and efficient way to join metal parts together? Look no further than welding! You know the significance of using the right tools and equipment to produce high-quality results as a skilled welder. That’s where we come in. A leading manufacturer of top-notch welders designed to meet your needs and exceed your expectations!
Welding is a versatile process vital in numerous industries, including construction, automotive, and manufacturing. It enables you to create strong, durable, and structurally sound connections between metal pieces, ensuring the integrity and longevity of your projects. Whether working on small-scale projects or tackling large-scale constructions, having a reliable welding machine can greatly enhance your efficiency and productivity.
Our welders are built with precision and durability in mind, crafted to ensure the utmost reliability and performance. No matter the type of welding technique you specialize in – MIG, TIG, or stick welding – we have the perfect equipment. From lightweight, portable machines that grant you unmatched mobility to heavy-duty models designed for maximum power, we have a broad selection to cater to your specific needs.
Investing in one of our high-quality welders enhances your capabilities and ensures your safety. Our machines are equipped with advanced safety features to protect you and others around you during the welding process. From thermal overload protection to ergonomic designs that reduce strain on your body, we prioritize your well-being to enable you to work peacefully.
Moreover, our welders are engineered to be user-friendly, allowing even novice welders to achieve professional-level results. With intuitive controls and clear instructions, you can quickly adapt to our machines and get to work efficiently. We understand that time is of the essence, so we have designed our welders to be incredibly reliable and easy to maintain so you spend less time on repairs and more time on what matters – welding!
Investing in a high-quality welder from our trusted brand is a decision that will benefit you in countless ways. From expanding your opportunities within your current field to opening doors to new industries, our welders can help you take your career to new heights. With our dedication to innovation and customer satisfaction, we are confident you won’t be disappointed with your choice.
Don’t settle for subpar welding equipment – choose a welder that reflects your professionalism and commitment to excellence. With our superior range of welders, backed by our solid reputation in the industry, you can trust us to provide you with the tools you need to achieve outstanding results. Join the thousands of people who have already experienced the difference our welders can make in their work and elevate your welding capabilities today!
Weld joint design
Are you ready to take your welding projects to the next level? One key aspect often overlooked is the importance of weld joint design. A well-planned and executed weld joint design can significantly impact the quality and strength of your welds.
So, what exactly is weld joint design, and why is it important? Put simply, it refers to how two metal pieces are prepared and positioned before welding. The right weld joint design ensures proper fusion between the metals, creating a sturdy bond that can withstand heavy-duty applications. On the other hand, a poorly designed joint may result in weak welds, compromising the overall integrity of your work.
Regarding weld joint design, there are various types to consider based on your specific needs. The choice of joint depends on factors such as the type of metal being welded, the thickness of the materials, and the desired strength of the weld. Selecting the appropriate joint to achieve the desired results and avoid unnecessary stress or failure.
Let’s explore some common weld joint designs that you may encounter in your welding projects:
1. Butt joint: This is one of the simplest and most commonly used joint designs. Two metal pieces are joined in a square or rectangular formation, forming a cross-section that resembles the letter “H.” It is suitable for materials with similar thickness and provides good strength.
2. Lap joint: In this design, one metal piece is placed over another, overlapping slightly. The result is a joint that looks like the letter “T.” Lap joints are often used when welding sheets or plates together and offer good resistance to twisting forces.
3. T-joint: As the name suggests, this design forms a “T” shape when two metal pieces are welded together. It is commonly used for joining two materials at right angles to each other and provides excellent strength and stability.
4. Corner joint: A corner joint is typically used when welding two metal pieces at a 90-degree angle. This joint design is ideal for fabricating boxes or square frames and offers strength and rigidity.
Remember, the success of your welding projects largely depends on the quality of your weld joint design. By taking the time to select the right type of joint and ensuring proper preparation and positioning, you can achieve welds that are not only visually appealing but also structurally sound. So, invest in a high-quality welder that meets your needs and provides the necessary features to execute various weld joint designs efficiently. With the right equipment, you can confidently create strong, durable welds that impress clients and peers alike.
Heat input control
Are you looking to improve your welding skills? One aspect you may not have considered is the importance of heat input control. While it may not be the most glamorous topic in the world of welding, it is certainly a crucial factor in achieving high-quality welds.
What exactly is heat input control, you may ask? Simply put, it is the ability to regulate the amount of heat applied during the welding process. This control allows you to achieve optimal weld penetration, minimize distortion, and produce reliable welds. And let’s be honest, people, these qualities matter in ensuring your welds’ longevity and integrity.
Now, you may be wondering how heat input control is achievable. The answer lies in investing in a high-quality welder that offers precise heat input adjustment. As a leading welder manufacturer, we understand the needs of welders like yourself. That’s why our welders come equipped with advanced heat input control features, empowering you to take full control over your welding projects.
With our welders, you can easily adjust the heat input settings to match the thickness and type of metal you work with. This ensures optimal fusion while avoiding excessive heat that can lead to distortion and weak welds. Think of it as having a fine-tuning knob for your welder, allowing you to work with confidence and precision.
You may still wonder why heat input control is so vital. Well, let’s break it down simply for you. A high heat input can negatively impact the mechanical properties of a weld, making it more prone to cracks, fractures, and failures. On the other hand, inadequate heat input can result in poor fusion, weak joints, and potential defects. Finding the right balance is essential.
Investing in a welder that offers reliable heat input control allows you to consistently achieve welds that are not only strong but also aesthetically pleasing. And let’s not forget about the time and cost savings! By avoiding unnecessary rework or repairs caused by heat-related issues, you can ensure that your projects are completed efficiently and within budget.
So, dear welder, don’t overlook the significance of heat input control in your welding endeavors. Make the smart choice and invest in a welder that puts the power of heat regulation in your hands. With our advanced heat input control features, you’ll be able to confidently tackle any welding project, knowing that you can produce top-notch welds every time. Trust us, people, your welding game will never be the same again!
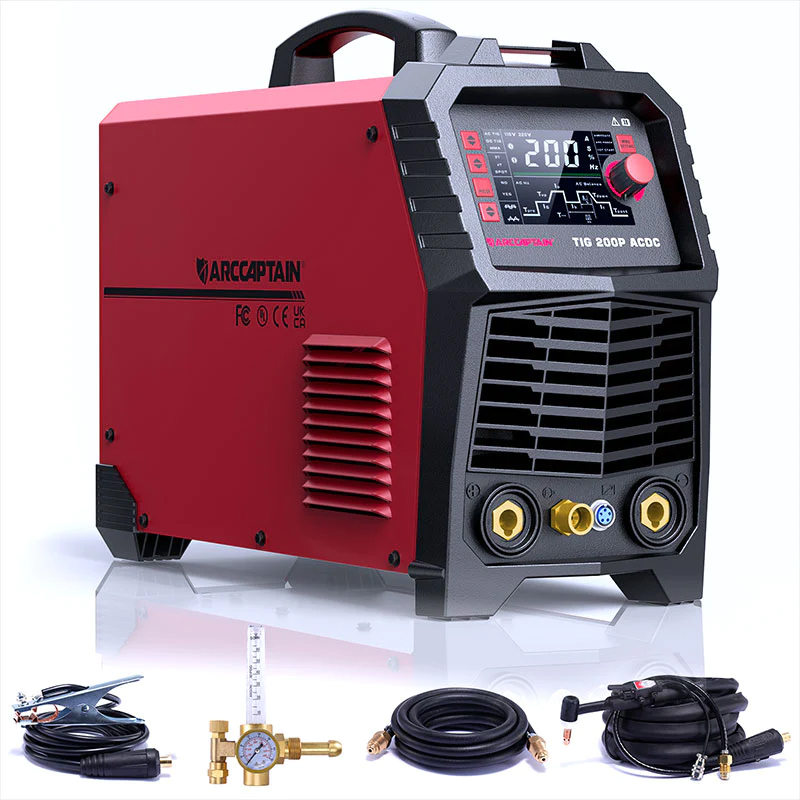
Welding machines used by Welders
Are you a welder looking for a reliable and efficient welding machine? Look no further! We understand that the tools you use are essential to your craft. That’s why we are here to introduce you to our top-quality welding machines built to meet your needs.
Our welding machines are designed to make your work easier and more efficient. With cutting-edge technology and precision engineering, they deliver exceptional results every time. Whether you are a professional welder or a DIY enthusiast, our machines are perfect for a wide range of welding projects.
One of the advantages of our welding machines is their versatility. They can handle different types of welding, including MIG, TIG, and Stick welding. This means they can tackle materials like stainless steel, aluminum, and carbon steel. No matter the project, our machines will provide you with the power and control you need to produce high-quality welds.
Durability is a key feature of our welding machines. We understand how important it is for your equipment to withstand the demands of your work. Our machines are built with robust materials and undergo rigorous testing to withstand any tough welding environment. You can trust that our welding machines will stand the test of time, giving you peace of mind and saving you money in the long run.
Safety is a top priority for welding, and our machines are equipped with advanced safety features. From built-in overheating protection to automatic shut-off mechanisms, we have taken every precaution to ensure your safety while operating our machines. Knowing that our machines prioritize your well-being, you can confidently focus on your welding tasks.
Another advantage of our welding machines is their user-friendly design. We understand that not everyone is an expert welder, and our machines are designed to be intuitive and easy to use. Whether you are a seasoned professional or just starting, our machines will make your welding experience smooth and hassle-free. They come with clear instructions and ergonomic handling, allowing you to concentrate on perfecting your welds.
Finally, we pride ourselves on providing excellent customer support. We value our customers and strive to assist them in any way we can. If you have any questions or need guidance regarding our welding machines, our knowledgeable and friendly team is here to help. We want to ensure you have the best welding experience possible.
Don’t waste any more time with unreliable and inefficient welding machines. Invest in a superior welding machine that guarantees top-notch results. Join the countless people who have trusted our welding machines for their needs. Take your welding skills to the next level with our exceptional machines. Explore our range of welding machines today and see the difference they can make in your welding projects!
Heat management techniques
Heat Management Techniques: Achieve Precision and Efficiency in Your Welding Projects
As a skilled welder, you know that effective heat management is key to ensuring successful and top-notch welding results. Whether engaged in large-scale industrial projects or working on smaller personal creations, having the right heat management techniques at your disposal is essential. With the right welding equipment, you can achieve precision and efficiency, giving you an edge in a competitive industry.
Understanding heat management and its importance:
Heat management is controlling and manipulating the temperatures generated during welding to achieve optimal results. This technique allows you, as a welder, to maintain the required temperature range and control the heat-affected zone (HAZ). Doing so can ensure proper fusion, reduce the likelihood of defects, and improve your welds’ overall quality and durability.
Utilizing different heat management techniques:
1. Preheating: Preheating involves heating the base material before welding. This technique helps to reduce the cooling rate and minimizes the risk of cracking or distortion. By controlling the initial temperature of the base material, you can achieve better control over the welding process, resulting in stronger, more reliable welds.
2. Post-heating: Post-heating applies heat to the welded joint after completion. This technique helps relieve residual stress and further enhances the weld’s mechanical properties. By applying controlled heat, you can minimize the risk of brittleness, increase the weld’s toughness, and ensure its long-term durability.
3. Heat Sink: A heat sink is a technique that involves using a heat-absorbing material to dissipate excess heat. By strategically placing heat sinks near the weld zone, you can prevent heat from spreading to unwanted areas. This technique ensures that critical components, surrounding materials, or delicate elements are not affected by excessive heat, allowing you to maintain the integrity of the final product.
4. Pulse welding: Pulse welding is a method that involves rapidly alternating between high and low heat settings. This technique helps manage heat input while preventing the base material from overheating. With pulse welding, you can achieve precise control over the amount of heat applied during the welding process and significantly reduce the chances of distortion or surface imperfections.
Invest in a reliable welding machine:
Investing in a high-quality welding machine is vital to effectively implementing these heat management techniques and delivering outstanding welding results. A top-of-the-line welder will provide precise temperature control, exceptional power output, and advanced features specifically designed for heat management. Look for welders with adjustable heat settings, pulse welding capability, and efficient cooling mechanisms to optimize your welding experience.
Ensure your success with superior heat management:
In conclusion, mastering heat management techniques is crucial for every welder. By employing these techniques, you can achieve superior weld quality, minimize defects, and enhance the mechanical properties of your welds. Remember, acquiring a reliable welding machine that gives you complete control over the heat input is key to success. Invest wisely, take control of your welding projects, and watch your efficiency and reputation soar as you deliver welding perfection every time!
Heat sink usage
Looking to enhance your welding skills and achieve flawlessly strong welds? Look no further! A heat sink is one tool that can make a significant difference in your welding projects. Now, you might be wondering, what exactly is a heat sink, and why is it essential for welders like you? Let us shed some light on this topic.
A heat sink is a vital accessory that helps control the temperature during welding, preventing the metal from overheating and protecting your workpiece. It absorbs and disperses excess heat generated during welding, ensuring a stable temperature and reducing the risk of deformation or damage to your project.
When it comes to effective heat dissipation, a reliable heat sink is your go-to solution. It acts as a heat conductor, drawing away excessive heat from the welding area and dispersing it throughout its surface. This helps maintain a controlled temperature, allowing you to produce consistent and high-quality welds.
But why should you consider using a heat sink in your welding endeavors? Here are some key reasons:
1. Avoiding Material Distortion: Excessive heat can cause the metal being welded to warp or deform, compromising the structural integrity of your workpiece. A heat sink efficiently pulls away this excess heat, minimizing the risk of distortion and ensuring a more precise and accurate weld.
2. Enhancing Weld Quality: Welding with a heat sink helps to maintain a stable temperature, reducing the chances of overheating. This controlled environment ensures that your welds are smooth, even, and free from defects such as porosity and cracks. By implementing a heat sink, you can achieve top-notch results that will impress you and others.
3. Expanding Application Possibilities: With a heat sink, you can venture into welding materials more susceptible to heat damage. Whether thin metals or heat-sensitive alloys, a heat sink offers the protection to comfortably weld these materials without compromising their structural integrity.
At our reliable welder manufacturing company, we understand the needs of welders like you. That’s why we offer many efficient heat sinks designed to meet your specific requirements. Our heat sinks come in various shapes and sizes, ensuring compatibility with various welding processes and projects.
Don’t let excessive heat hinder your welding journey. Invest in a high-quality heat sink today and witness the remarkable difference it makes in your work. Trust us, responsible welders know the significance of a well-regulated temperature, and a heat sink holds the key to achieving professional-level results while safeguarding your materials.
Take your welding game to the next level – choose our reliable heat sinks and weld like a pro!
Preheating and post-heating requirements
Are you a welder looking to enhance your welding projects? If so, understanding the importance of pre and post-heating requirements is essential for achieving the best results. These heating processes may not be the most glamorous aspects of welding, but they play a crucial role in ensuring the longevity and quality of your weld.
So, why should you bother with preheating? Imagine this scenario: you’re working on a steel fabrication project and start welding without preheating the metal. As a result, the cold temperature of the steel causes rapid cooling, leading to the formation of brittle welds. These weak welds are prone to cracking and breaking under stress, compromising the structural integrity of your work.
Preheating the metal can prevent this issue. Preheating involves gradually heating the base metal before starting the welding process. This process helps alleviate thermal stress and reduce the risk of cracking. It also ensures better weld penetration and minimizes the chances of weld defects, saving you time, effort, and money in the long run.
Now, let’s talk about post-heating. Once you’ve completed your weld, completing the project and moving on is not simple. Remember that your weld needs time to cool down gradually and evenly. Post-heating helps achieve this by applying controlled heat to the weld zone. This gradual cooling process eliminates the formation of unwanted stress and promotes the desired metallurgical structure of the weld.
Additionally, post-heating is crucial for reducing the risk of hydrogen cracking. During welding, hydrogen molecules can become trapped within the weld, weakening its integrity. Post-heating allows the hydrogen to escape slowly, preventing the formation of cracks and ensuring a stronger, more reliable weld.
Now that you understand the significance of preheating and post heating, you may wonder how to carry out these processes efficiently. This is where having a high-quality welder becomes indispensable. A reliable welder will offer precise temperature control, allowing you to achieve the necessary preheating and post-heating requirements accurately.
Investing in a professional-grade welder can make all the difference in your welding projects. Not only will it ensure that you can meet your materials’ preheating and post-heating needs, but it will also provide you with consistent and reliable performance for years to come. Remember, people who take their welding seriously understand the value of using the right tools, and a top-notch welder is one of them.
So, if you’re ready to take your welding skills to the next level, don’t overlook the importance of preheating and post-heating. Invest in a quality welder that will help you achieve optimal welds, ensure the longevity of your projects, and set yourself apart as a skilled welder in the industry. Your future welding projects and clients will thank you!
Challenges in welding thin to thick sections
Are you a welding enthusiast looking to improve your skills? Are you facing challenges when welding thin to thick sections? Well, you’re in the right place! At Arc Captain, we understand the hurdles people often encounter in this specific welding technique, and we have just the solution for you.
Welding thin to thick sections is a demanding task that requires precision and expertise. It involves seamlessly fusing materials of different thicknesses to ensure a strong and durable bond. However, achieving a high-quality weld in such scenarios can be challenging, even for experienced welders.
One of the major obstacles in welding thin to thick sections is achieving proper heat control. The thin sections heat up quickly, while thicker sections take time to reach the desired temperature. This temperature difference creates difficulties maintaining an even heat distribution, leading to potential welding defects.
Another common challenge welders face is achieving good fusion between the different thicknesses. As the welding progresses, the welder must maneuver through layers of varying heat conductivity and melting points. This requires skillful techniques to ensure proper fusion, avoiding discontinuities or weak bonds that could compromise the structural integrity of the weld.
Moreover, controlling distortion is another concern when welding thin to thick sections. The inherent difference in thermal expansion rates of dissimilar materials can cause warping or bending of the welded joint. This affects the weld’s aesthetic appeal and poses potential structural weaknesses.
However, fear not! Arc Captain offers a comprehensive range of welding machines that can easily tackle these challenges. Our advanced welders have cutting-edge features designed explicitly for welding thin to thick sections.
These welders offer precise heat control mechanisms, allowing you to regulate the temperature accurately along the entire weld seam. With our machines, you can maintain optimal heat distribution, ensuring the perfect fusion of materials of different thicknesses.
Additionally, our welders offer advanced waveform technology that enhances the bonding process for dissimilar materials. This technology allows for better synchronization between the weld pool and heat input, resulting in uniformly strong welds. With our machines, achieving proper fusion across different thicknesses has never been easier.
Moreover, our welders also provide innovative features such as adaptive welding programs that automatically adjust welding parameters based on the material thickness. This functionality significantly reduces the chances of distortion, resulting in a visually appealing weld while maintaining structural integrity.
In conclusion, welding thin to thick sections can present its fair share of challenges. However, these challenges become surmountable with Arc Captain’s cutting-edge welding machines. Invest in one of our reliable and high-performing welders today, and elevate your welding skills to new heights. Don’t let the complexities discourage you; let our welders be your trusted companion in confidently conquering any welding project.
Distortion risk
Title: Reduce Distortion Risk with Our High-Quality Welders
Introduction:
Are you a skilled welder seeking a reliable tool that respects your craft? Look no further! Our top-of-the-line welders are designed to minimize distortion risk when working on various metal fabrications. With our cutting-edge technology and dedication to quality, we prioritize your satisfaction while ensuring optimal welding results. Learn why our welders are the perfect choice to minimize distortion risks during welding projects.
Distortion Risk: A Common Roadblock for Welders:
Throughout your welding career, you have likely encountered the potential challenge of distortion. Distortion occurs when the welding process causes metal pieces to undergo dimensional or shape changes due to heat-induced expansion and contraction. While some degree of distortion is common in welding, it can hinder the precision and functionality of your final work, leading to potential setbacks. Luckily, our advanced welders are designed to mitigate distortion, enabling your work to shine without compromise.
How Our Welders Minimize Distortion:
1. Consistent Heat Control:
Our welders have cutting-edge technology that ensures precise, consistent heat control during welding. By maintaining a stable temperature throughout the welding process, our machines reduce thermal stress on the metal, minimizing the risk of distortion. With this level of control, you can confidently weld intricate structures, knowing that distortion will be minimal.
2. Superior Arc Stability:
The stability of the welding arc plays a vital role in controlling distortion. Our welders incorporate innovative features that provide superior arc stability, allowing for more controlled heat application. The uniform and reliable heat distribution keeps metal deformation at bay, making our welders an ideal choice to tackle even the most challenging fabrication projects.
3. Efficient Cooling System:
Preventing overheating is essential to minimize the risk of distortion during welding. Our welders come equipped with efficient cooling systems that dissipate excess heat produced during welding. This advanced cooling mechanism aids in maintaining the structural integrity of the metal, ultimately reducing distortion and ensuring the longevity of your welder.
4. Versatile Welding Modes:
Our welders offer a range of specialized welding modes suited to various metal types and project requirements. By adapting the welding mode to match the metal’s unique properties, you can achieve better control over the entire welding process. This customization further minimizes distortion risks, allowing you to produce the finest quality welds consistently.
Conclusion:
As a skilled welder, you understand the importance of high-quality equipment to optimize your craft. Our welders are carefully engineered to reduce distortion risks, prioritizing the precision and durability of your work. Equipped with cutting-edge technology, our welders boast consistent heat control, superior arc stability, efficient cooling, and versatile welding modes. Choose our welders, and confidently tackle any fabrication project, knowing that distortion will no longer impede your progress. Invest in our premium-grade welders today and take your welding expertise to the next level!